ERP solutions streamline manufacturing operations, balancing standard functionality with essential customisation. While out-of-the-box features enable faster deployment and cost savings, customisation supports unique workflows and business growth. However, excessive modifications can increase costs and maintenance challenges. The key is partnering with ERP experts to optimise functionality without unnecessary complexity.
ERP to Maximise Equipment Uptime
Managing Maintenance Activities Seamlessly
In today’s highly competitive industrial landscape, equipment uptime is a critical factor that directly impacts productivity, cost-efficiency, and customer satisfaction.
Unplanned equipment downtime can lead to significant financial losses and operational disruptions.
To address this challenge, many organisations are turning to predictive maintenance (PdM) strategies, coupled with Enterprise Resource Planning (ERP) system integration, to maximise equipment uptime.
In this article, we will explore how PdM and ERP integration can work together to achieve this goal.
What is Predictive Maintenance?
Predictive maintenance is a data-driven maintenance approach that aims to predict when equipment is likely to fail so that maintenance activities can be scheduled proactively. It relies on various technologies such as sensors, IoT devices, and advanced analytics to monitor equipment health in real-time.
By analysing real-time data from equipment, PdM systems can identify patterns and anomalies that indicate potential issues. This information allows maintenance teams to schedule activities more efficiently, reduce downtime, extend equipment lifespan, and lower overall maintenance costs.
Let’s take a closer look at the core components of predictive maintenance.
Data Collection: Sensors and IoT devices collect data on equipment performance, temperature, vibration, and other relevant parameters.
Data Analysis: Advanced analytics, machine learning algorithms, and artificial intelligence (AI) are used to process the collected data, identifying patterns and anomalies that indicate potential issues.
Predictive Models: Predictive models are developed to forecast equipment failure and recommend optimal maintenance actions.
Condition Monitoring: Continuous monitoring of equipment conditions helps in assessing when maintenance is needed.
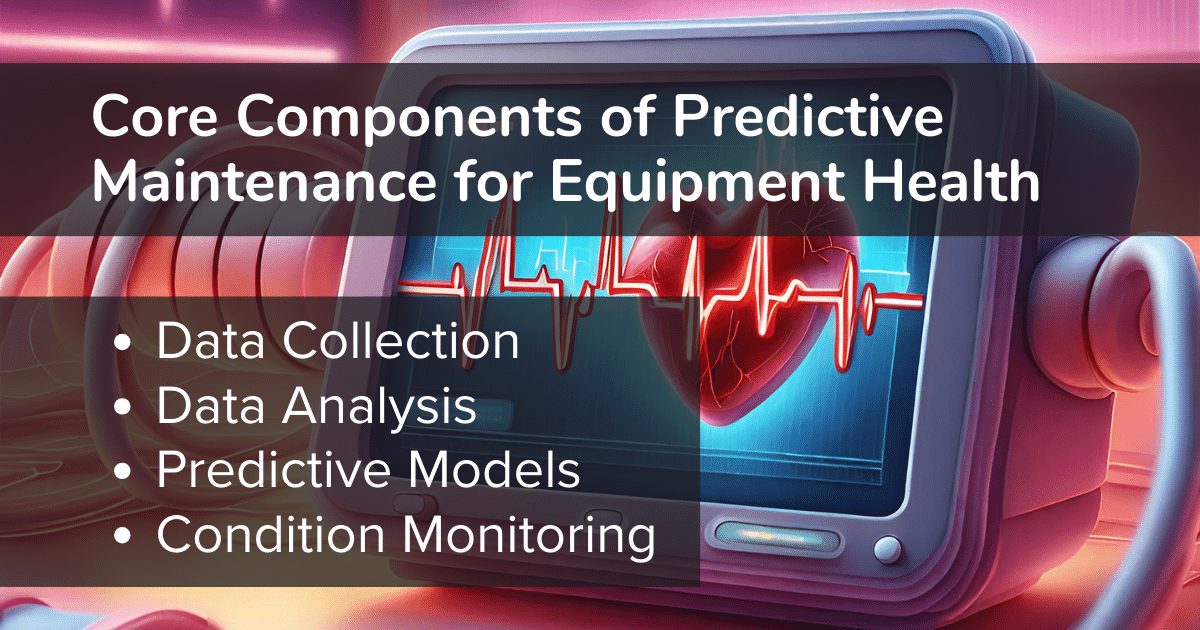
Predictive Maintenance and ERP Integration
ERP systems are powerful tools that integrate various business processes and functions, including finance, inventory management, human resources, and maintenance.
Integrating predictive maintenance into an ERP system means combining the capabilities of PdM technologies with the functionality of an ERP software platform to create a seamless and comprehensive solution for managing maintenance activities within an organisation.
A centralised ERP platform that combines predictive maintenance capabilities with broader business management functions can achieve several overarching organisational benefits.
Centralised Data: ERP systems provide a centralised repository for all data related to equipment, maintenance history, and operational metrics. This allows for a holistic view of equipment performance.
Real-Time Insights: ERP systems can be configured to receive real-time data from predictive maintenance sensors, enabling instant visibility into equipment conditions and performance.
Streamlined Workflows: Maintenance workflows can be automated and streamlined within the ERP system, making it easier to schedule maintenance activities and allocate resources efficiently.
Predictive Analytics: Integrating predictive maintenance algorithms into the ERP system allows for predictive insights to be seamlessly incorporated into maintenance planning and scheduling.
Achieving Maximised Equipment Uptime
Integrating predictive maintenance with an ERP system is a powerful strategy for achieving maximum equipment uptime. It combines real-time monitoring, data analysis, and proactive maintenance planning with broader business processes and resource management.
Here’s how the combination of PdM and ERP integration helps maximise equipment uptime:
Early Fault Detection
- Predictive maintenance uses sensors and data analytics to monitor equipment in real-time. By integrating this data with the ERP system, early signs of equipment degradation or faults can trigger automatic alerts and notifications.
- Maintenance teams can address issues proactively, often before they lead to unplanned downtime.
Scheduled Maintenance
- ERP systems, when integrated with PdM data, can schedule maintenance activities at optimal times, considering equipment availability and production schedules.
- This ensures that maintenance does not disrupt critical production periods and minimises the impact on uptime.
Data-Driven Decision-Making
- The integration of PdM with ERP allows organisations to make data-driven decisions about maintenance priorities, resource allocation, and equipment replacement.
- Maintenance strategies can be optimised based on historical data and predictive insights, leading to better uptime outcomes.
Inventory Management
- ERP systems can manage spare parts and inventory efficiently. When integrated with PdM, the ERP can automatically trigger inventory replenishment based on predicted maintenance needs.
- This reduces the risk of downtime due to unavailability of critical spare parts.
Optimised Workforce Deployment
- Predictive maintenance alerts, when integrated into ERP, can help organisations allocate maintenance personnel more effectively.
- Maintenance teams can be dispatched to address critical issues promptly, minimising downtime associated with equipment failures.
Performance Metrics and KPIs
- Integration allows for the tracking of key performance indicators (KPIs) related to equipment uptime, mean time between failures (MTBF), mean time to repair (MTTR), and other relevant metrics.
- This enables organisations to set targets, monitor progress, and continuously improve uptime performance.
Resource Efficiency
- Predictive maintenance integration with ERP reduces the need for routine, calendar-based maintenance. Maintenance tasks are performed when data indicates they are necessary, optimising resource usage.
- This results in cost savings and maximises the availability of maintenance personnel for critical tasks.
Downtime Analysis and Reporting
- When downtime does occur, the integrated system can capture detailed data about the event, including the cause, duration, and impact on operations.
- This information is valuable for root cause analysis and process improvement efforts to further reduce downtime in the future.
Predictive Maintenance Feedback Loop
- Integrating ERP with predictive maintenance creates a feedback loop where historical data and maintenance outcomes can be used to continuously refine predictive models and maintenance strategies.
- This iterative improvement process leads to higher equipment reliability and reduced downtime over time.
By continuously analysing data and adjusting maintenance schedules, organisations can maintain and continue maximised equipment uptime while achieving productivity improvements such as reduced equipment downtime, decreased maintenance costs, increased overall equipment efficiency, and extended lifespan for critical equipment.
As smart manufacturing technology continues to advance, the synergy between predictive maintenance and ERP systems will become even more vital in achieving productivity and operational goals.
Inspired to Act?
Book a Discovery Call with one of our product specialists to learn more about how an ERP system can transform your business.
Subscribe to our LinkedIn Newsletter and get alerts when we post about topics that matter to you.
Related Articles
Epicor ARM 2024.2.2 Released
Unlock smarter procurement with Epicor ARM 2024.2.2! From flexible approval workflows to seamless invoice matching, this release is packed with customer-focused improvements to boost efficiency and control. Discover how the latest Epicor ARM enhancements can streamline your procurement and AP management, making it smarter, faster, and more efficient!
The Hidden Risks of Managing Business Processes with Spreadsheets
Spreadsheets have long been a go-to tool for managing business processes, but as companies grow, they often expose hidden risks. While spreadsheets might work for small-scale tasks, relying on them for critical business operations can lead to inefficiencies, errors, and data security issues. To stay competitive and efficient, businesses must explore more robust solutions like ERP software. In this blog, we’ll look at the most common problems with spreadsheets and how enterprise resource planning solutions offer a better way to manage business processes.
Most Common Problems With Inconsistent Business Processes & How To Fix Them
Inconsistent business processes can slow down operations, increase costs, and lead to inefficiencies. Identifying and fixing these issues is essential for smoother operations. Here are the most common problems with inconsistent processes and how ERP software solutions can help address them.
Unlock Seamless UI Testing with Kinetic’s Test ReCoder Tool
Kinetic customers can now harness the power of the Test ReCoder UI Test Tool to set their QA processes on a smarter, faster track! This core enhancement in the latest Kinetic release (2024.2) is loaded with benefits including reduced test execution time, lower error rates, and enhanced productivity.
Enhancing Process Efficiency: Proven Strategies, Essential Tools, and Best Practices
Efficient processes drive business success, enabling companies to streamline operations, cut costs, and improve productivity. To achieve process efficiency, businesses need a combination of the right strategies, tools, and practices. In this guide, we will explore how ERP software solutions with industry-specific tools can enhance your operational efficiency.